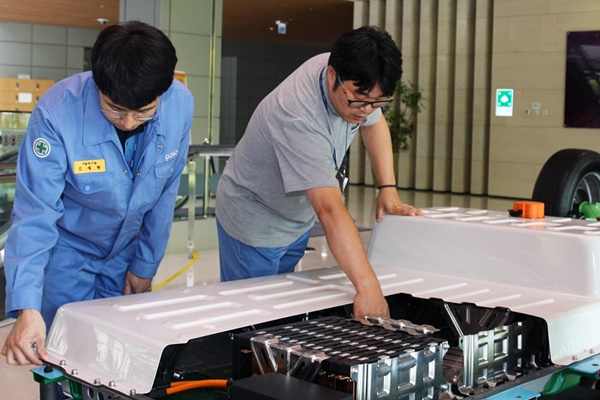
[이코노믹리뷰=이가영 기자] 전기차와 수소차 등 친환경차 시장이 급격하게 성장하면서 철강업계의 소재 경량화 경쟁이 본격화하고 있다.
친환경車 시장 성장… 소재 경량화 ‘화두’
6일 업계에 따르면 최근 몇 년간 전기차와 수소차 등 친환경차 시장이 급격하게 성장하고 있다. 하나금융연구소에 따르면 2012~2016년 동안 전 세계 자동차 판매 가운데 친환경차 비중은 2%에 불과했지만 2017년 3.6%, 2018년 4.8%, 2019년 5.7%로 늘었다.
시장에서는 친환경차 시장의 성장이 앞으로도 가속화될 것으로 보고 있다. 정부의 탈 탄소 기조 아래 친환경차 구매보조금 지급, 면세 혜택 등 정책이 늘고 제조사들과 소비자의 인식이 변화할 것으로 전망돼서다. 코로나19 이후 환경정의에 대한 관심이 늘고 있는 점도 친환경차 시장 성장 가능성을 더하고 있다.
실제 한국자동차산업협회에 따르면 지난해 전 세계 자동차 판매량이 급감한 가운데서도 전기차 판매량은 사상 최고치를 기록한 것으로 추산된다. 협회는 향후 10년 간 친환경차 시장이 연평균 20~30% 성장해 전체 자동차 시장 내 비중이 20% 이상을 차지할 것으로 전망하고 있다.
친환경차 성장이 커지면서 소재 경량화에 대한 관심도 늘고 있다. 연비 효율성과 직결된다는 점에서다. 전기차의 경우 배터리와 구동 모터가 추가되면서 전체 무게가 늘어날 수밖에 없다. 이에 바디나 서스펜션 등이 가벼워져야만 기대하는 수준의 연비 효율성이 가능해진다. 통상 전기차에 탑재되는 배터리는 400~500kg, 모터와 전장류는 150kg 정도로 알려진다.
소재 경량화는 철강업계의 주요한 화두로 떠오르고 있다. 통상 일반 자동차 총 중량의 약 60%는 차제 부품과 프레임 같은 철강제품으로 구성되기 때문이다. 기존 철강 제품을 더 가볍게 만들어야만 차량 경량화가 가능해진다.
일례로 배터리와 구동모터를 사용하는 친환경차에서는 자동차에 사용되는 전체 철강재 가운데 25~30%를 차지하는 엔진, 변속기 등의 파워트레인 부품이 불필요하다. 기존의 주력 소재인 특수강 수요는 줄어들 수밖에 없다. 반면 차량 바닥면에 배치되는 배터리팩을 보호하기 위해 기존 제품 대비 가볍고 인장강도가 높은 초고장력강판 수요는 늘어나고 있다.
특히 엔진 대신 전기 구동 모터가 사용되고 핵심부품으로 배터리가 장착되면서 전기 에너지를 효율적으로 사용가능한 전기강판의 사용이 확대되는 추세다. 통상 기존 내연기관차에는 5kg 정도만 투입되는 전기강판이 친환경차에서는 전체의 50%이상 투입된다.
아울러 자동차의 바디나 섀시, 트렁크 등 다양한 부분에서 기존 일반강판을 대체하는 알루미늄 활용도 늘고 있다. 탄소섬유강화플라스틱(CFRP)의 경우 높은 가격에도 불구하고 무게가 가벼워 활용범위가 더욱 늘어날 것으로 전망된다.
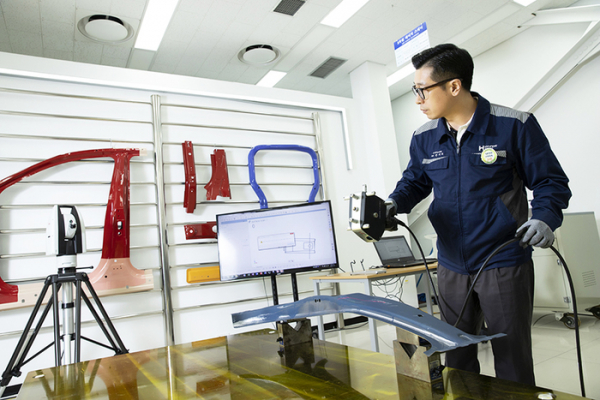
포스코·현대제철, 소재 경량화시장 선점 사활
주요 전방 산업이 자동차 시장의 판도가 달라지면서 철강사들도 발빠르게 소재 경량화에 나서고 있다. 특히 전체 수익 가운데 고부가 제품인 자동차 강판이 차지하는 비중이 30%가 넘는 포스코와 현대제철은 소재 경량화 추세에 대응에 적극 나서고 있다.
포스코는 친환경차와 관련 전기차의 무게를 획기적으로 줄일 수 있는 기가스틸, 무방향성 전기강판(Hyper NO) 등 친환경차 소재를 타깃으로 한 철강 제품을 집중 개발해 왔다.
기가스틸은 1㎟ 면적당 100kg의 이상의 무게를 견딜 수 있는 초고장력강판이다. 십원짜리 동전만한 크기에 25톤 이상의 무게를 버틴다. 알루미늄, 탄소 섬유 강화 플라스틱 등 보다 더 강하고 가벼운 소재인만큼 훨씬 가벼운 차체를 구현할 수 있다는게 포스코의 설명이다.
기가스틸은 경제적이며 환경친화적이다는 특징도 갖는다. 포스코에 따르면 기가스틸은 알루미늄과 비교해 소재 가격은 3.5배, 가공비는 2.1배나 낮다. 또한 자동차의 누적 CO2 배출량을 기존 대비 약 10% 감소시켜 환경을 보호하는 효과도 있다.
아울러 무방향성 전기강판은 에너지 손실을 최소화 할 수 있다. 전기차에는 자동차의 엔진에 해당하는 구동모터가 탑재된다. 구동모터의 효율을 향상하려면 전력 손실이 낮은 전기강판이 요구된다. 포스코 Hyper NO는 전기에너지를 회전에너지로 변화시키는 과정에서 필연적으로 생기는 에너지 손실을 최소화하고 효율성을 높일 수 있도록 개발됐다. 포스코에 따르면 Hyper NO는 기존의 전기강판 대비 에너지 손실이 30%이상 낮다.
현대제철 또한 경량화 소재 시장 선점을 위한 개발과 생산에 집중하고 있다.
현대제철은 국내외에 핫스탬핑 생산라인을 갖추고 있다. 핫스탬핑은 950°C의 고온으로 가열된 철강소재를 금형에 넣고 프레스로 성형한 뒤 금형 내에서 급속 냉각시키는 공법이다. 이를 통해 가볍고 인장강도가 높은 초고장력강을 만들 수 있다. 다른 경량화 소재 대비 비용도 저렴하다.
이를 통해 TWB 핫스탬핑 차체 부품용 1㎬ 소재 개발에도 성공했다. ㎬ 소재는 외부 충돌에 버티는 차량 뼈대 역할을 하는 센터필러를 만드는 데 쓰인다. ㎬는 재료 강도를 측정하는 단위로, 1㎬는 가로세로 1㎜ 크기 재료가 100㎏ 무게를 버틸 수 있는 강도로 기존 자동차 외부 판재보다 2~5배 강하다.
전기차에 적용되는 스틸 배터리 케이스 개발도 마쳤다. 알루미늄 배터리 케이스와 무게는 비슷하지만 원가는 15%가량 낮다. 중량을 줄이기 위해 초고장력강판을 적용했으며 내연성도 알루미늄보다 높아 안전성도 끌어올렸다는 평가다.
철강업계 관계자는 “철강사들의 친환경차 시장에서의 소재 경량화 경쟁은 더욱 심화될 것으로 보인다”며 “복합소재가 각광받으면서 독자적 기술 개발 물론 기술력 있는 소재 기업과의 전략적 제휴를 통해 경량화에 대비하는 기업들도 속속 생겨날 것”이라고 전망했다.